|
|
Biscuit and Chocolate production line - Hony and Chocolate |
|
|
|
|
|
Chocolate & Fruity Top Souce Production Line
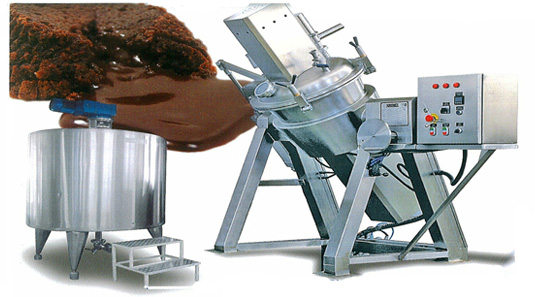
|
|
|
|
|
Fruity Jell Production Lines
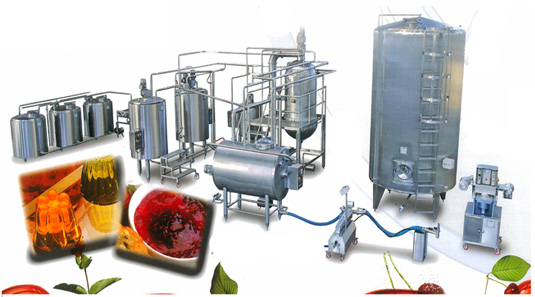
|
|
|
|
|
|
Chocolate & Fruity Jelly Production Lines
Technical Data
* Chocolate production line:-
- Machine and equipments for production of chocolate
- Process lines capacity range goes from 500LT/day to 20000LT/day
- Special chocolate process tanks, liqueur mixing tank, melting vats, chocolate tables with heating and without heating for stretching of special chocolate
* Fruity jelly production line:-
- Machines and equipments for fruity jelly.
- Fruity jelly. Production lines capacity range goes from 1000LT/day To 5000 LT/day
*Chocolate Process Tank:-
- Capacity : from 1000 LT To 20000 LT
- Type : Vertical cylindrical isolated, serpantined , epecial stirrer
- Cover : Collapsible cover
- Accessories : Product inlet-out let valve, thermometer, PT 100 , sight glass, CIP muzzles
*Fruity jelly volumetric filling system
- Working system : possibility to fill as a volumetric filling bypriston
- Dosing Capacity: from 1 LT to 13 LT
- KRMJ-Fruity Process System with Vacuum
- Type: Horizontal cylindrical
- Isolated, special designed stirrer, vacuum system, inverter speed adjustem, plat form
- Cover: Manhole cover with EPDM rubber gasket for food stuffer automatic controlled steam and water inlets, sight glass, illumination, adjustable feet
|
|
|
|
|
|
Grape Moulasses Production Lines
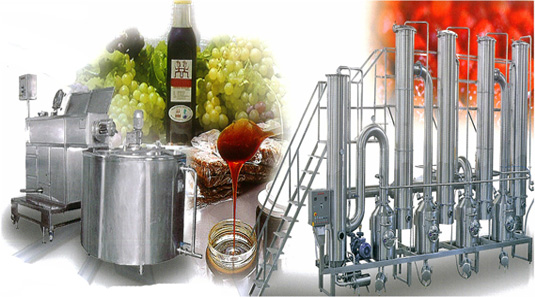
|
|
|
|
|
|
Grape Malasses Production Line
Technical Data
- All machines and equipments for Dried Grapes, Data, Apple, pear and Grape molasses production lines.
- Production equipments Capacity range goes from 500 LT to 5000 LT
- Special designed process tanks, product conveyor, mincing machines (for dried grape) squeezing machines, vacuum evaporator, pneumatic filling units.
Process Tanks
Vertical type process tanks suitable for total daily product capacity.
It’s serpontined, isolated, law stirrer, break water, thermometer, CIP inlet, product out let, collapsible cover
DRIED DRAPE SQUEEZING MACHINE
- Intimae circulation squeezing, press system, Trans faring pump residue out let cap, manhole cover, special helical squeezing system, unfermented grape dice out let cap, adjustable food.
GRAPE MOLASSES VACUUM EVAPORATOR
- Capacity: 500 LT/h , 1000 LT/h , 2000 LT/h , 3000 LT/h , 5000 LT/h
- Type : continuo’s type evaporators
- To supply increasing of the solid rate
- inlet unfed mended grape juice rate 13%
- out let grape molasses rate 70%
- Continuo’s type evaporators are consist of film evaporation towers
- Expansion towers and expansion’s tubes
- in the system , pumps with water cooling for unfermented grape juice Transfer, feeding and vacuum pumps for unfermented grape juice transfer and condense sucking are existed
- Fillings and pipe lines are on the continue evaporator CIP unit and evaporators can be designed CIP unit or without CIP unit
|
|
|
|
|
|
Tahina Halava Production lines
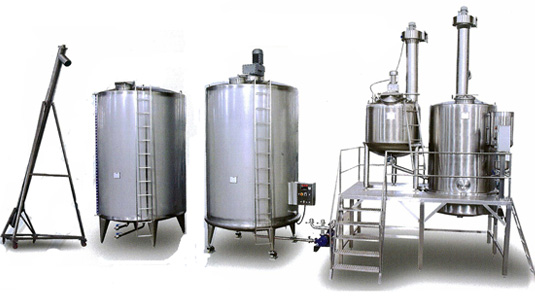
|
|
|
|
|
|
Tahina Halva Production Line
Technical Data:
- All machines and equipment for Halva production lines
- Tahina (Sesame Oil) Halva production lines capacity range goes from 350 lt to 5000 lt
- Syrup preparing tanks, capacity range goes from 1000 lt to 20000 lt according to total / daily capacity, Serpantined, heating with oil, special mixer and load cell are exited
- KRH Halva process system:
It is supply to produce of white wax for halva production portable syrup carrying conveyor for feeding of KRH Halva process system
Tahina (sesame oil) Halva production line
1- Glucose Storage Tank
2- Sugar Syrup Preparing Tank
3- Soap root Tank
4- KRH Halva Process Tank
KRH Halva Process System
- Capacity: 350 Lt/40 min
- KRH Halva process system is consist of syrup cooking tank (1000 Lt), product preparing tank (3000Lt), Electricity panel and platform
- Syrup cooking tank supply to mix of sugar, glucose and water by means of its special stirrer wings
- Product preparation tank supply to obtain of homogenized white wax by mixing of syrup and soap root
- Special impeller system, it is supply to take vapor of product during the operation
- Special Heat system, it has oil heating that supply to prevent of bumming of sugar |
|
|
|
|
|
Milky Dessert Production Lines
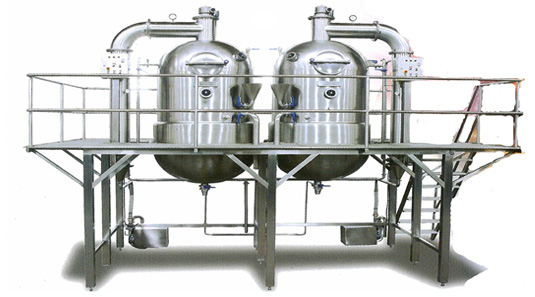
|
|
|
|
|
|
Milk Dessert Production Line
Technical Data
- All machines and equip ments for cream powder, chicken breast pudding, Nuh`s, rice pudding, Rice Pudding, milk pudding with coconut etc….
- 300 LT/h, 500 LT/h, 1000LT/h, 1500LT/h and 2000LT/h capacities
Production
- Single or continue vacuum evaporators according to total product capacity
- Volumetric filling system which prevent to damaging of product’s structure
- CIP system for total production lines capacity
Milky desserts production line
- Milk Reception Tank
- Milk Storage Tank
- Evaporation Unit
- Filling Hopper
- Volumetric Filling System
- CIP unit
Milk Desserts Evaporation system
- Capacity: Evaporation system supply to reach desired brix without damaging of products structure
Evaporators can be produced as single or continue according to total product capacity of 500, 1000, 1500, 2000, 3000, 5000 Lt/h
- Type: Vertical Cylindrical
- It is consist of vacuum pump , cooling tower, mixer, inverter speed adjustment platform
- Cover: Men hole cover with EPDM rupper gasket for foodstuffs
- Accessories: Electrical control panel, CIP caps, PT 100, Monometer, sampling valve, illumination lamp, Air Hole, Sight Glass, Discharging valve.
|
|
|
|
|
|
Sesame Reception, Stroing, Wetting, Peeling, Washing Unit
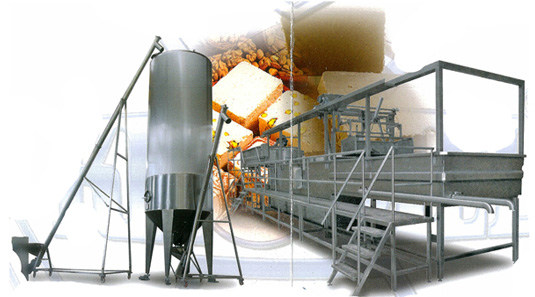
|
|
|
|
|
|
Jam & Marmaled Production Lines

|
|
|
|
|
|
|